Piston fillers
Doselite
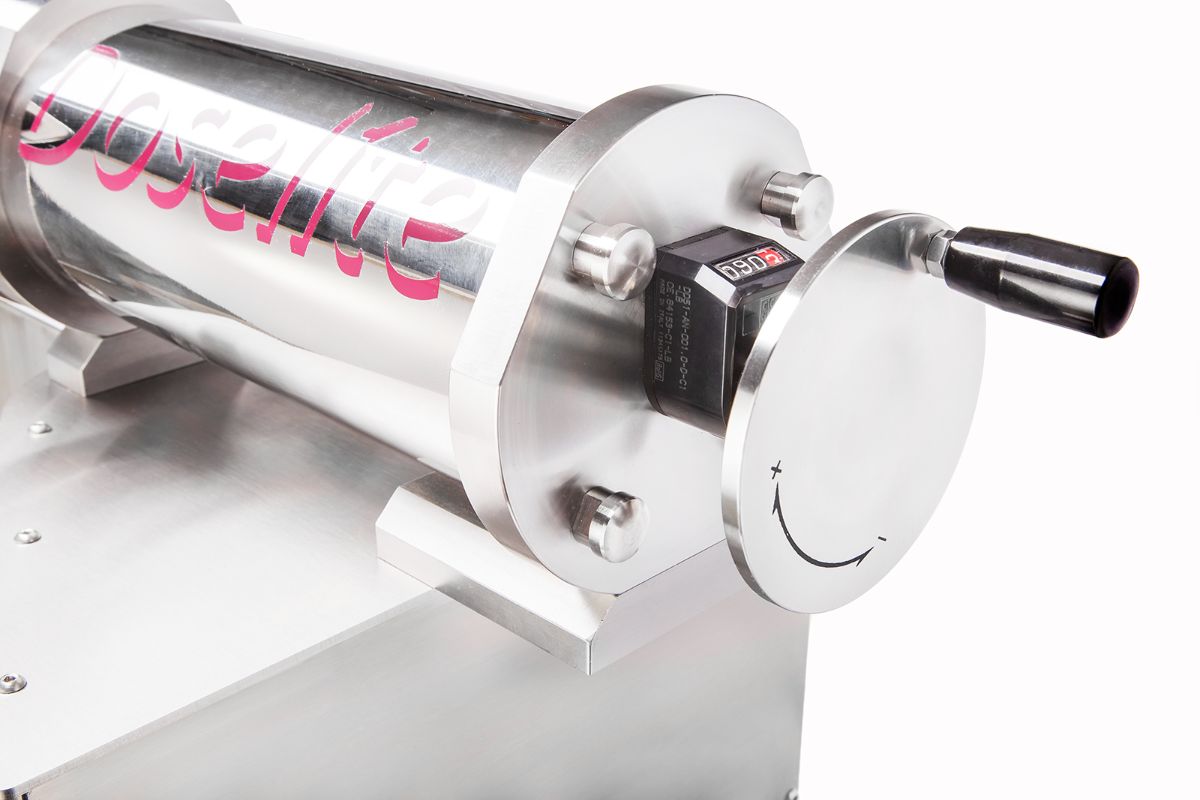
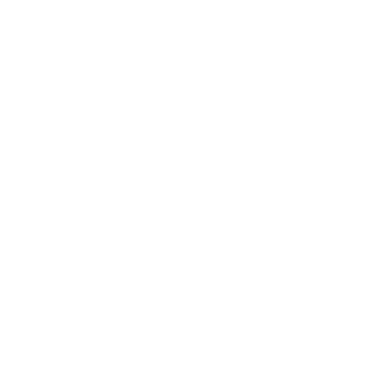
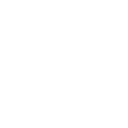
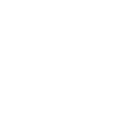
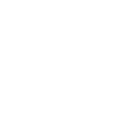
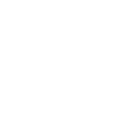
Pneumatically operated volumetric dosing machines, of extreme precision, reliable and easy to use, for the packaging of liquid, semi-dense and even highly dense products, with and without suspended pieces, in any type of container.
Doselite dosing pumps offer:
- Extreme precision in dose repeatability
- Versatility: all parts in contact with the product are made of AISI 316 stainless steel; therefore, they are indicated for use in the food sector, for the packaging of sauces, jams, pesto, meat sauce, yoghurt, mayonnaise, ketchup, and in general for pet food in cream or sauce, chemistry, for the packaging of solvents, paints, varnishes, pastes, resins, glues, in the field of cosmetics and herbal medicine for the packaging of creams, perfumes, nail polishes and gels, shampoos, scrubs, oils, masks, liquid foundations, mascaras, lip glosses and of the pharmaceutical industry for the packaging of creams, syrups, liquid and thick preparations for pharmaceutical and veterinary use.
- Wide range of controls that allow you to check and intervene on pressure, temperature, dispensing speed and suction speed.
- Flexibility and ease of use, materials and specific certifications make the Doselite range the most suitable and professional solution for any packaging line
All Tenco dosing syringes can be moved pneumatically or via brushless motors, the latter guaranteeing even more precision in dosing and can be perfectly integrated into automatic production lines. Doselite can also be customized according to needs with a base to be positioned on a bench or trolley with dosing pump at the top or bottom or, again, integrated into automated packaging lines.
The dosing pistons can also be equipped with resistances to keep the product at a predefined temperature and they can still be combined with simple loading hoppers, heating groups, mixers or pressing systems, to facilitate the aspiration of the product to be dosed. Ultimately, each machine can be built with the most suitable configuration for the specific needs of the user.
Technical specifications
Some technical data to know more about Doselite
Specifications
- about 350/400 jars per hour (variable production depending on the type of product and the speed of the operator)
- 30 l/m for 40 cc - 100 cc and 250 cc models
- 90 l/m for 380cc - 680 cc and 1300 cc models
- pneumatics
- 40 cc model 780 X 326 X 515 mm h
- 100 cc model 780 X 326 X 515 mm h
- 250 cc model 780 X 326 X 515 mm h
- 380 cc model 846 X 326 X 565 mm h
- 680 cc model 846 X 326 X 565 mm h
- 1300 cc model 846 X 326 X 565 mm h (in the bench version)
- trolley version: 813 X 500 X 1300 h (all versions)
- 40 - 100 and 250 cc counter models: 25 kgs
- 380 - 680 and 1300 cc models: 35 kgs
- wheeled model: 50 kgs (all sizes)
- 4-6 bars
Configurations
- from 0-40 cc
- from 2 to 100 cc
- from 5 to 250 cc
- from 5 to 380 cc
- from 20 to 680 cc
- from 50 to 1300 cc
- from 50 to 1500 cc
- micro-cylinder available up to 7 ml
- on bench
- on low trolley
- on high trolley
- PTFE food
- HPU and PTFE food
- HPU food
- PTFE
- PTFE and EPDM
- 3-way dispenser valves
- 2-way check valves
- feed hoppers
- anti-foam spouts
- stainless steel clamps
- food dispenser feed hoses
- hot product feed hoses
- chemical feed hoses
- supply hoses for solvent products
- stainless steel fittings
- 2-way non-return valves in steel
- 2-way non-return valves in plastic
- anti-drip kit
- gasket kit for food
- gasket kit for chemical/cosmetic products
- gasket kit for solvent based products
- bottom fill nozzle kit
- hopper mixing system kit
- dosing heating system kit
- hopper heating system kit
- kit valve heating system
- pipe heating systems kit
- antifoam device kit
- hopper pressing system kit
Packaging
- bottles
- jars
- plastic bottles
- jerry cans
- plastic jars
- PET bottles
- PET trays
- PET jars
- flexible bags without spout
- flexible bags with already welded spout
- aluminum trays
- metal cans
- tinplate cans
- bottles
- jars
- bottles (frugalbottle)
- trays
- jars
Video Gallery
To see Doselite in action in various versions and for different applications, you can explore our video library.
FAQs
Do you still have any doubts? Here you will find all the answers you need.
Yes, our Doselite piston doser can be used for the packaging of any liquid or dense product, even at high temperatures (over 100 degrees). All gaskets in contact with the product are made of food-grade silicone and PTFE (depending on the type of product to be dosed) and every part in contact with the product is made of 316L stainless steel, so they can work without problems with any type of product, even at high temperatures.
The quantity of product (volume of product) to be dispensed is easily selected using the dose adjustment handwheel which is positioned on the back of the dosing pump. The handwheel adjusts the stroke of the piston and consequently the volume to be dispensed. There is also a reference numeric counter to increase or reduce the stroke cycles of the piston and, consequently, the quantity of product to be dispensed.
For the filtration of some liquid products it is also possible to insert a filter holder at the inlet of the Doselite volumetric doser. This filter holder must also be equipped with filter cartridges (available in fiberglass and steel). The filter cartridges to be used with Doselite have the same characteristics as those used with Enolmatic and Enolmaster, however they are not the same, as they have different dimensions.
The Doselite is fully pneumatic in operation, therefore no electrical power supply is required, but it does require a compressor or compressed air system. We recommend using a compressor with the following minimum requirements: tank capacity 80 Lt, air flow 300 litres/minute, power 1.5Hp, possibly silenced and absolutely not lubricated. It is advisable to use an anti-condensation filter or a dryer to avoid any damage to the pneumatic components in case of particularly humid environments.
What is the maximum viscosity that can be dosed with Doselite?
The viscosity of the products to be treated varies greatly and can depend on different factors. In fact, it is possible to use systems for pressing, heating or mixing the product and this can facilitate the aspiration of the product itself. For the dosage of a product at room temperature, it is generally possible to indicate a maximum viscosity of 50,000 cPs. However, it is always advisable to send a sample of the product to be tested in the workshop.
All available configurations
The machine can be configured on demand to meet all needs
Over-the-counter doses
The Doselìte volumetric piston dosers can be customized according to the needs of use, with a base to be positioned on a bench or on a trolley with wheels, with a dosing pump at the top or bottom or, again, …
Doselite on trolley with wheels
Kit and accessories
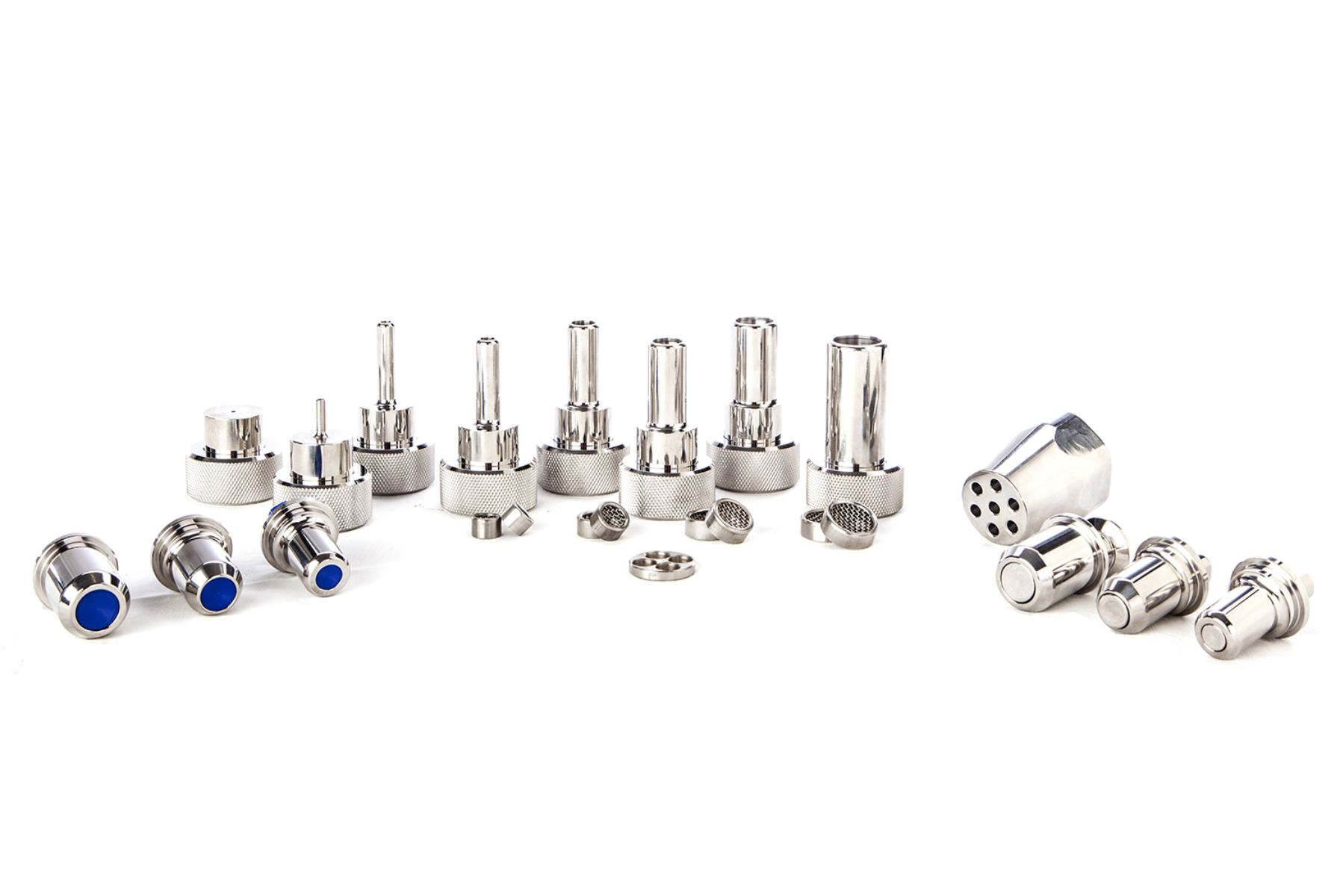
Anti-drip kits and systems
Interchangeable anti-drip systems to be combined with metering valves for volumetric feeders.
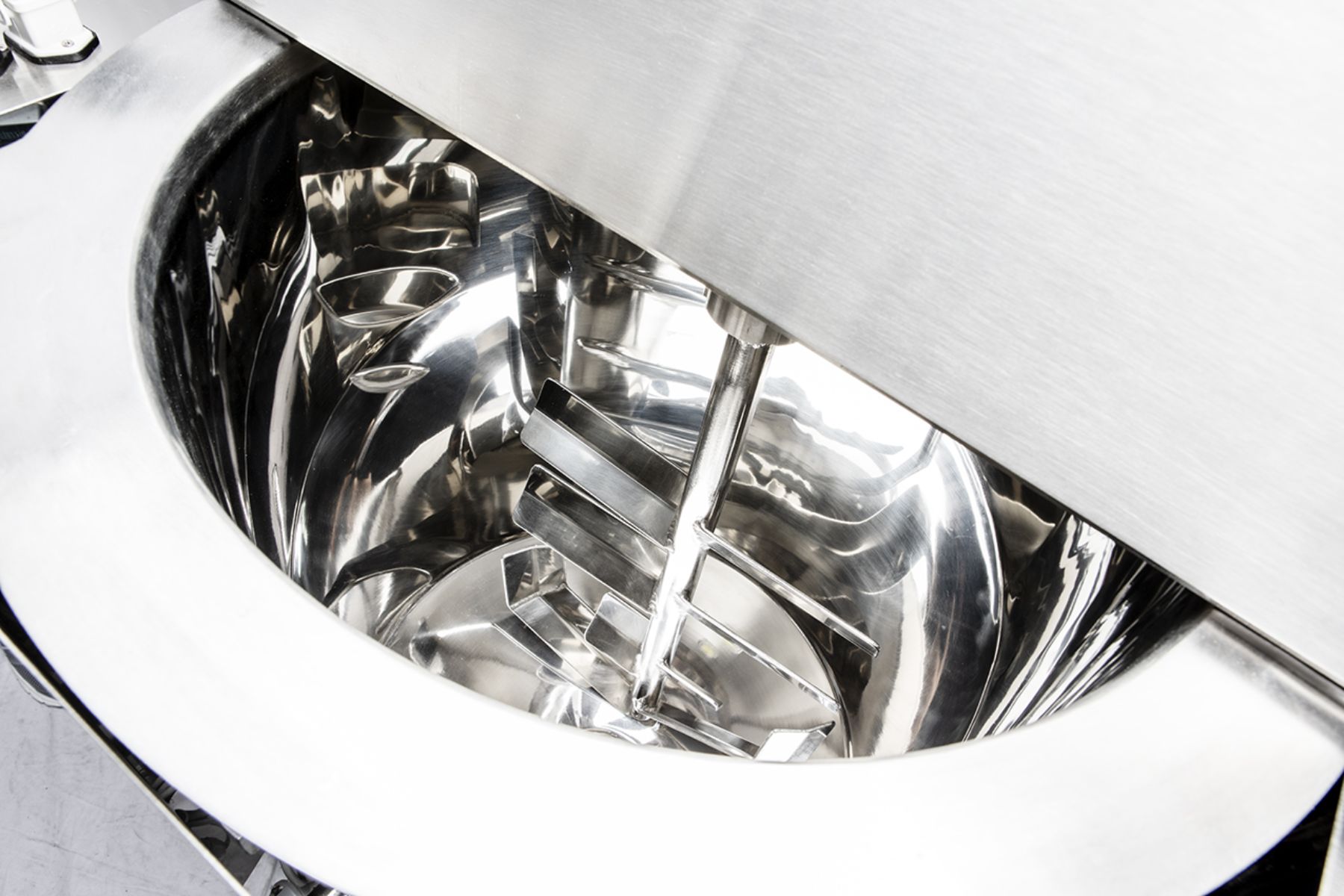
Product loading hopper
Product loading hoppers for volumetric feeders. Custom-built and configurable with numerous accessories.
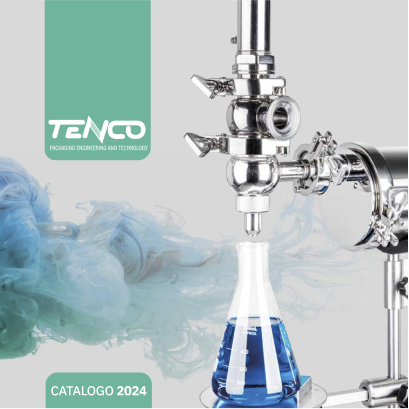
Products that might interest you
Discover all the filling products similar to Doselite
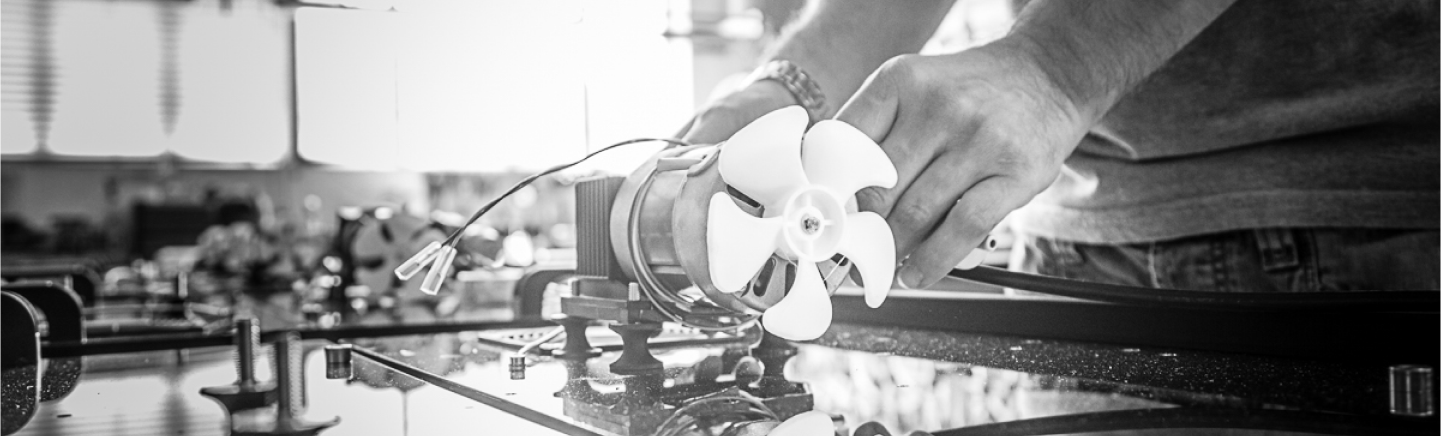
Talk to a consultant
Need specific information about this machine? Enter your email address to be contacted by a specialized consultant